Steve Rainey is the test pilot for the largest airplane in the history of the world in terms of wingspan, and he has made it clear that operating it comes with its fair share of intricacies.
The behemoth, owned by Stratolaunch, is known affectionately as the Roc — named after a bird of giant proportions from ancient mythology. It was originally designed to launch payloads into orbit, but now, Rainey and his team are aiming for the Roc to launch recoverable hypersonic vehicles that the aerospace industry will use for high-speed flight testing.
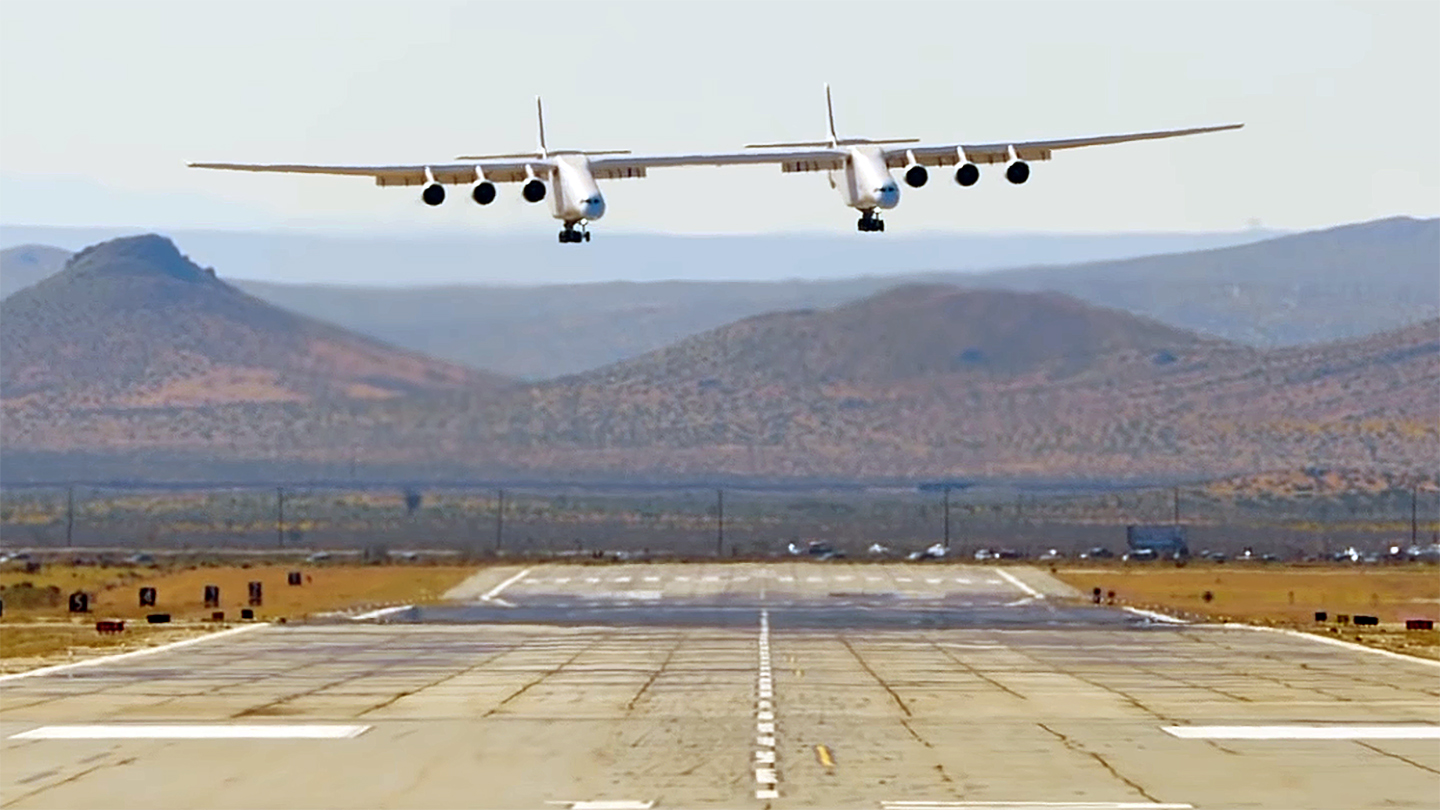
Rainey went into detail about his experiences with flying the Roc during a lecture hosted by the Western Museum of Flight in late January of this year. Rainey has a decorated past in the U.S. Air Force and as Lockheed Martin’s chief test pilot for the F-22 Raptor. But in 2022, he joined Stratolaunch, three years after the Roc’s first flight test out of the Mojave Air and Space Port. He has since been involved in six of the aircraft’s nine total flight tests in various roles ranging from pilot to mission director.
The Roc was designed and built for Stratolaunch by a separate company, the famed Scaled Composites, which gave the aircraft its official Model 351 designation. Roc has a 385-foot wingspan, a max gross take-off weight of 1.3 million pounds, and is powered by six Pratt & Whitney PW4056 turbofan engines that are normally found on the Boeing 747-400. Combined, those engines provide a staggering 336,000 pounds of thrust. That’s equal to nearly five F-22 Raptors with their twin F119 engines all in full afterburner.
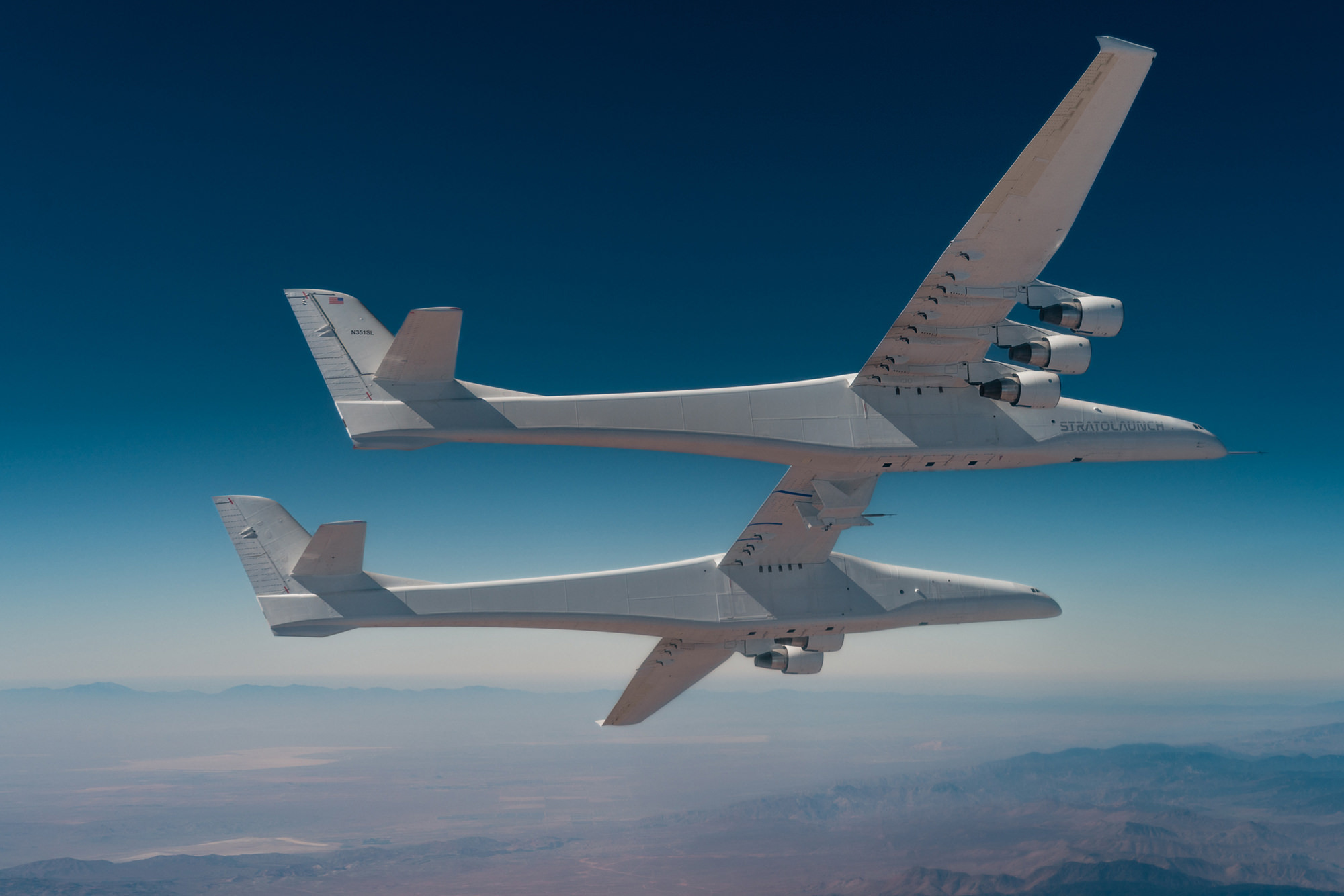
The Roc’s gargantuan composite airframe, featuring a unique twin-fuselage design, comes together to make for a very interesting flight experience and piloting challenge, as told by Rainey.
“It’s a big, big airplane with 12 banks of ailerons, 14 banks of flaps, four elevators, and [the crew] is on the right-hand side,” said Rainey. “You would think that the control forces would be very, very high, but they’re actually not. The cabling system uses some metal cables, but we use some advanced composite cables for most of it. It’s the same stuff that racing sailboats use, and that’s better for cable stretch at various altitudes and temperatures. And then over the pulleys where we have pulleys or meets or junction boxes, that’s done with actual metal cables there.”
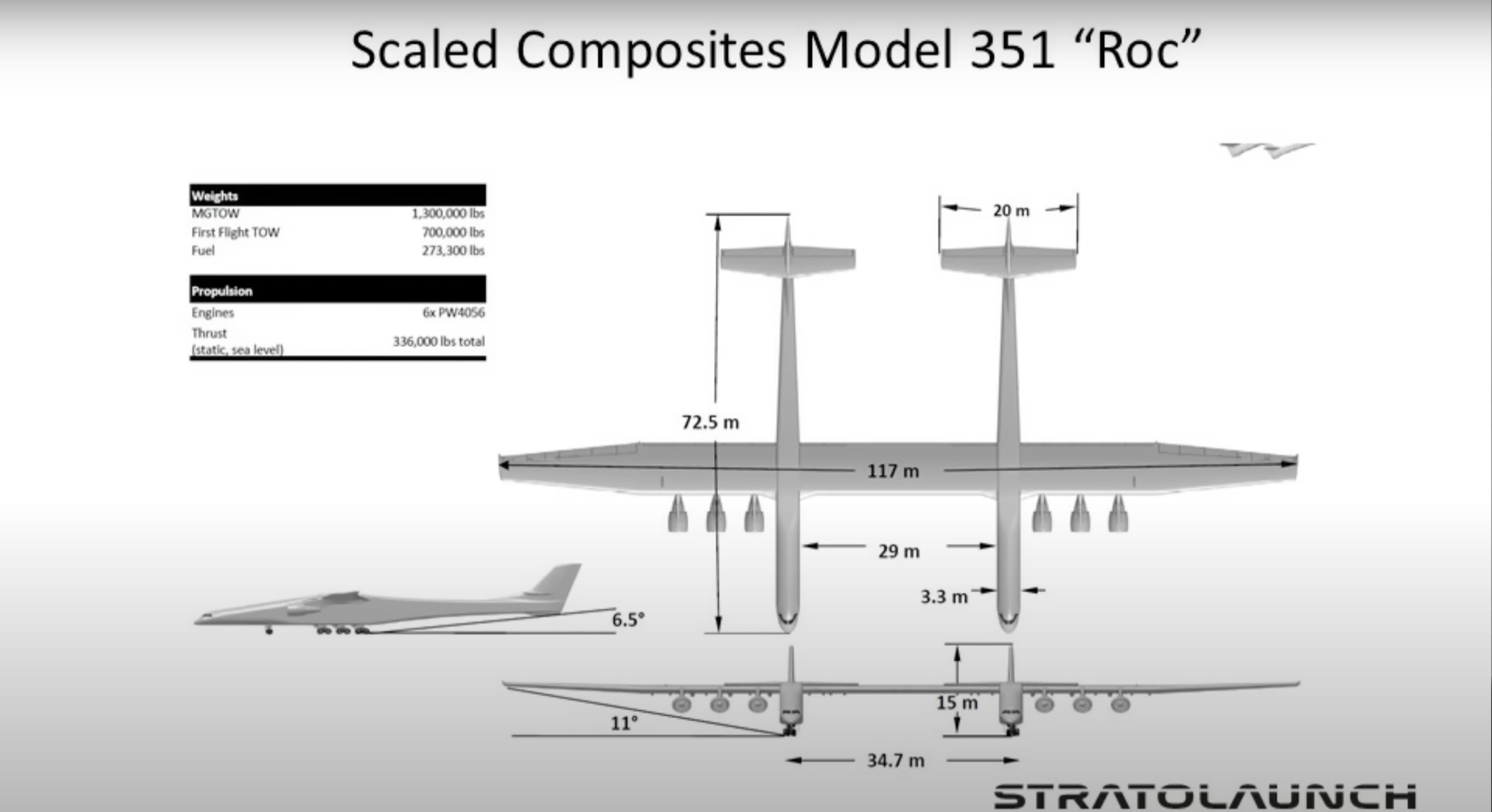
The Roc’s construction makes for a bit of a wild ride, as well. Rainey admits, “One thing I didn’t anticipate was the motion that’s going on within that composite airplane. You feel a little bit of everything, and you’re moving around pretty good.”
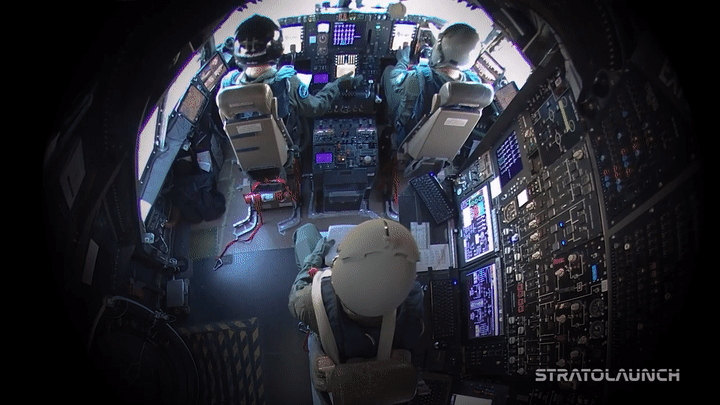
Landing the world’s biggest plane also comes with its own set of nuances. First and foremost, the Roc’s landing gear is spaced extremely wide, approaching that of the entire runway’s width.
“For the pilots here, it’s 114 feet from the left edge of the left gear to the right edge of the right gear truck,” said Rainey. “So, you can imagine … We have almost zero error margin when landing the airplane. So, landing the airplane can be quite an emotional event, especially if you’ve got any turbulence or winds coming along.”

Inside the Roc’s right-side fuselage is the flight crew, which includes two pilots and a flight engineer who can also act as the payload operator. The fuselage on the left, while pressurized, has no seats or cockpit and is instead full of various avionics equipment. Only electrics and pneumatics are shared between the fuselages, with fuel being split separately amongst the wings, according to Rainey.
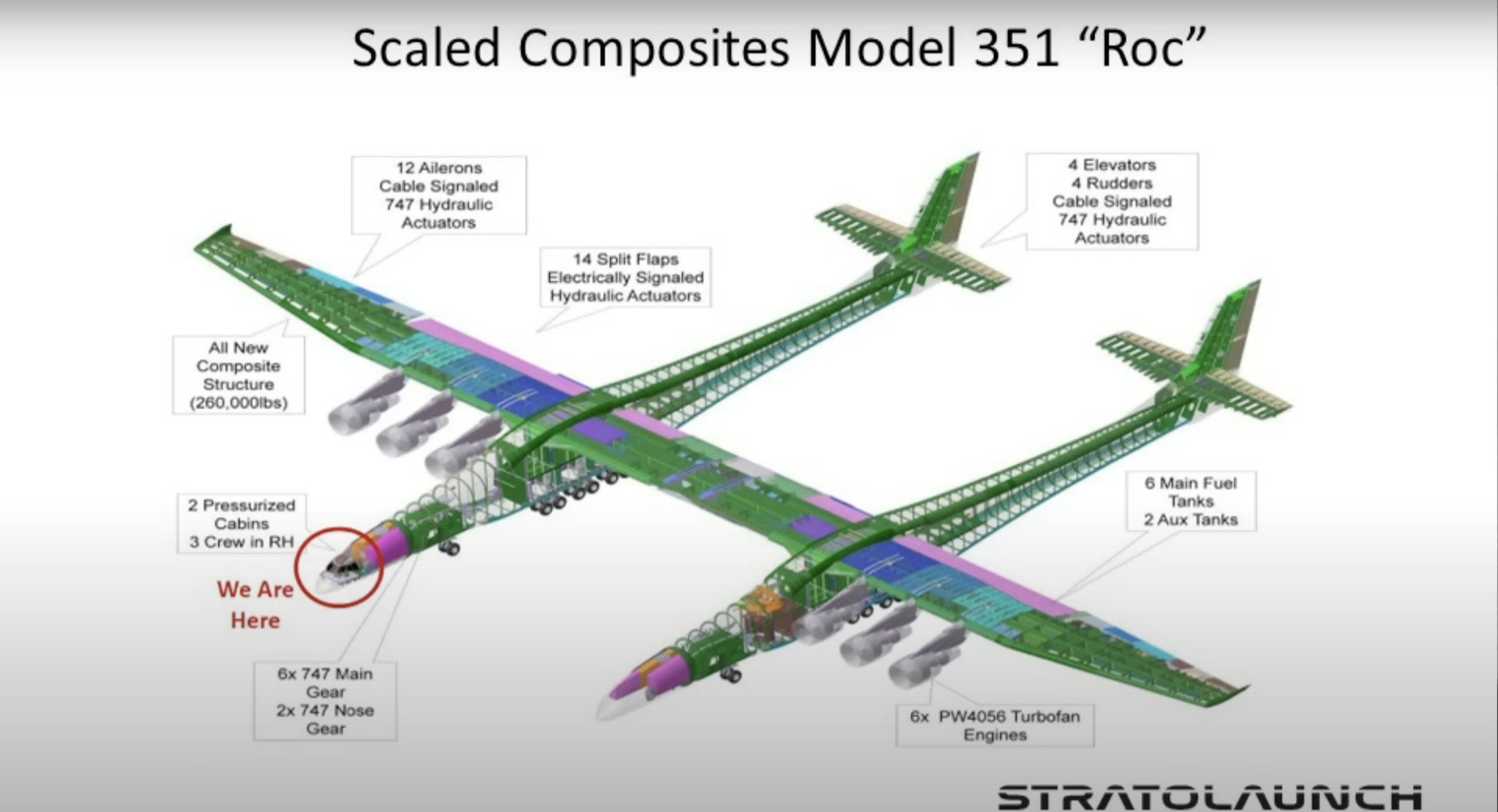
“Because of the distance between those fuselages, it is very very critical on takeoff and landing that [they] are pointed exactly straight down the runway,” Rainey said. “Any deviation more than a few degrees and guess what? You’re gonna go four-wheeling with the Roc, and that’s not something we want to experiment with.”
Both the pilot and the co-pilot can take over certain flight controls to ensure that the main focus remains on keeping the Roc as aligned as possible on approach and during take-off.
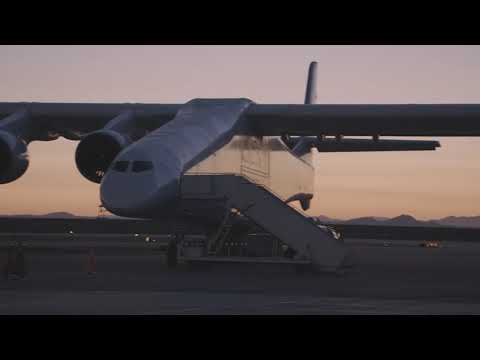
“Largely the design is such that things are split,” Rainey said. “So, for instance, the pilot cables — yeah we’re ‘fly by wire’ alright, fly by cable — so it’s literally a cable system … and through a pogo system just like the 747 underneath the floor, underneath the pilots, those are connected so that we both control the whole airplane. The beauty of that is if something goes wrong, we can disconnect them and still fly the airplane with one side adequately.”
When landing, the way the Roc divvies up duties between operators can also help take the pressure of calculating things like the ‘crab angle’ off of the pilot. During an approach with crosswinds, the crab angle is formed when the aircraft is cocked into the direction of the wind so that its ground track remains in line with the runway.
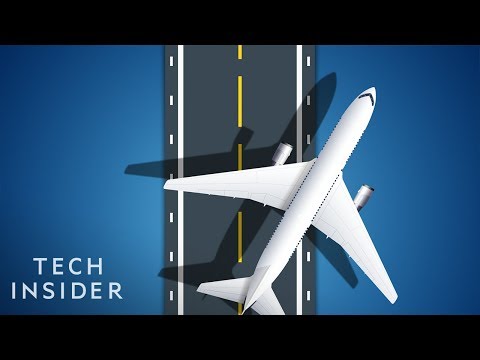
“So during landing, since I told you it’s kind of an emotional event, what’s the pilot got to do? Obviously, a two-man airplane and so one thing we have found is the engines are fairly stable and you don’t have to move them that much, but when it’s important, it’s important,” Rainey explained. “It is very easy to get fixated on say pitch or where I am in reference to my black line or what is the crab angle of the airplane, and you don’t want to do that. So, we’ve offloaded some of that in that the pilot is not flying, but the co-pilot, he controls the throttle … And so the pilot has to worry about his aim point.”
The Roc also utilizes flashing cues that come together to help Rainey and his co-pilot better visualize all that goes into getting the giant aircraft on the ground safely.
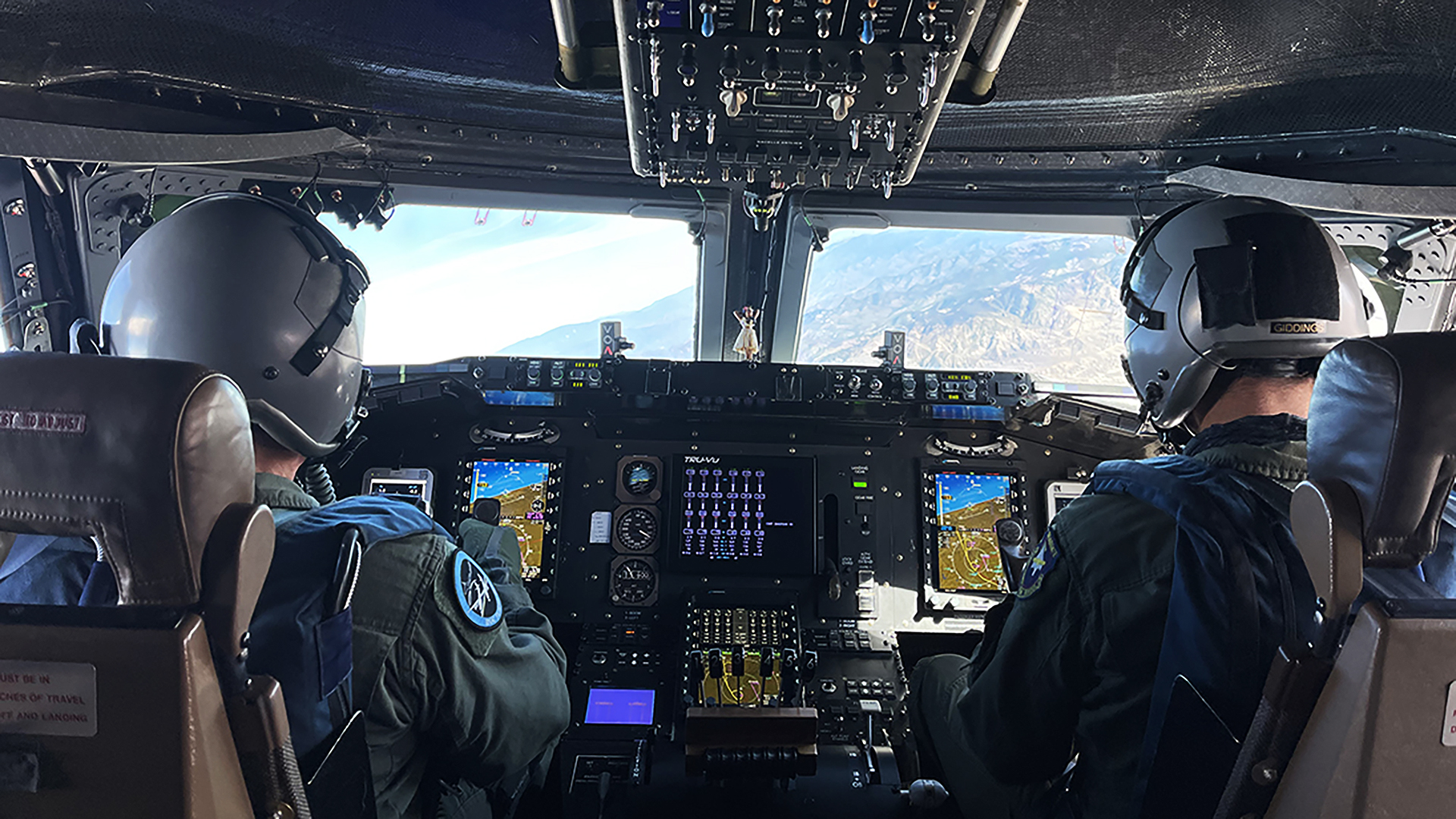
“We’ve got some lights across, right in front of the pilot and copilot, we call it the ‘crab-o-meter,’ and it is very sensitive,” Rainey said. “We set in the actual runway heading. So, for instance, runway three zero at Mojave is actually 303, so we set that in and the crab-o-meter has various lights to tell us the deviation from 303 degrees. So, we line up on the black line, we make sure that we got 303 set, we use bank angles … We don’t want to have any crab at all, and we make sure we land with no lights on the crab-o-meter, and if you get one, you’re probably going around or at least you got your hands full correcting that situation.”
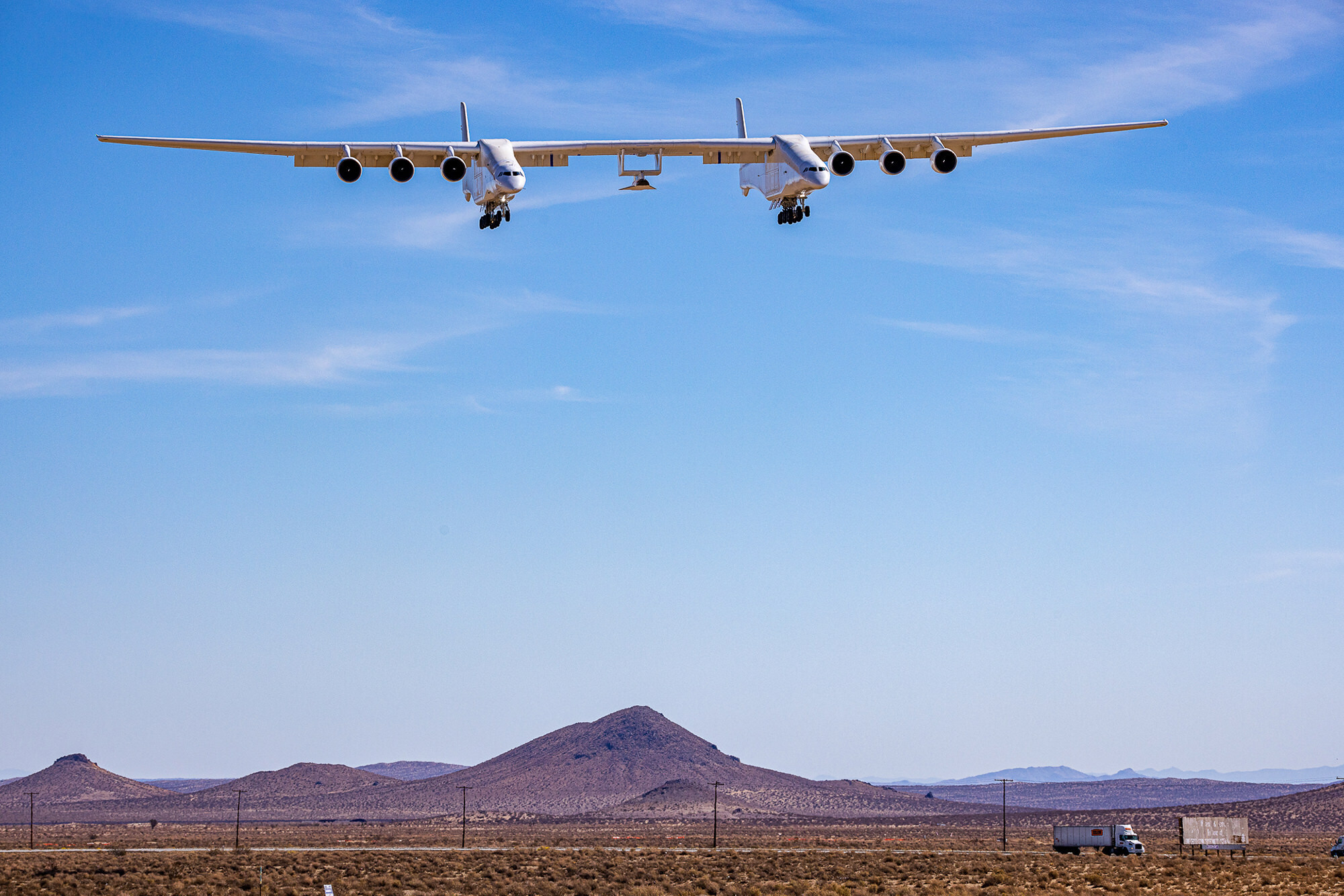
The Roc has even incorporated technology inspired by devices aboard U.S. military aircraft to help keep the giant steady and prevent its tail from smacking the runway on landing.
“Normally flying around, we’re at about, depends on the speed, but we’re a very low pitch angle, and we’ve got basically from about zero to six degrees to land this airplane,” Rainey said. “Air Force airplanes have this thing we call an ‘angle of attack indexer.’ Well, we stole that and we use it for pitch angle. And in fact, after flight five, I changed it so that it gives us a little bit more feedback. It used to just go off when we hit, like, four degrees. And so now I have it graduating, doing some flashing at the upper chevron, and when you get within a degree of hitting the tail, the whole thing’s gonna flash at you.”

Along with its PW4056 engines, the Roc has been designed with a number of additional parts and components taken from the Boeing 747, some of which contribute to how the aircraft performs. For instance, 747 landing gear door actuators have been used for the Roc’s huge flaps.
“Landing gear actuators only have two positions, open and closed, as do our flaps, zero or 70,” Rainey said. “So, I was telling these guys, I’ve got a straight-wing Cessna 180 at home with a STOL [short takeoff and landing] kit on it, and if I throw the 40 flaps down and walk in the hangar and blow on it, it’s likely to fly. So, you can imagine with 385 feet of that and 70 degrees of flaps, [the Roc] always wants to fly and it is very affected by the air mass that’s around it.”
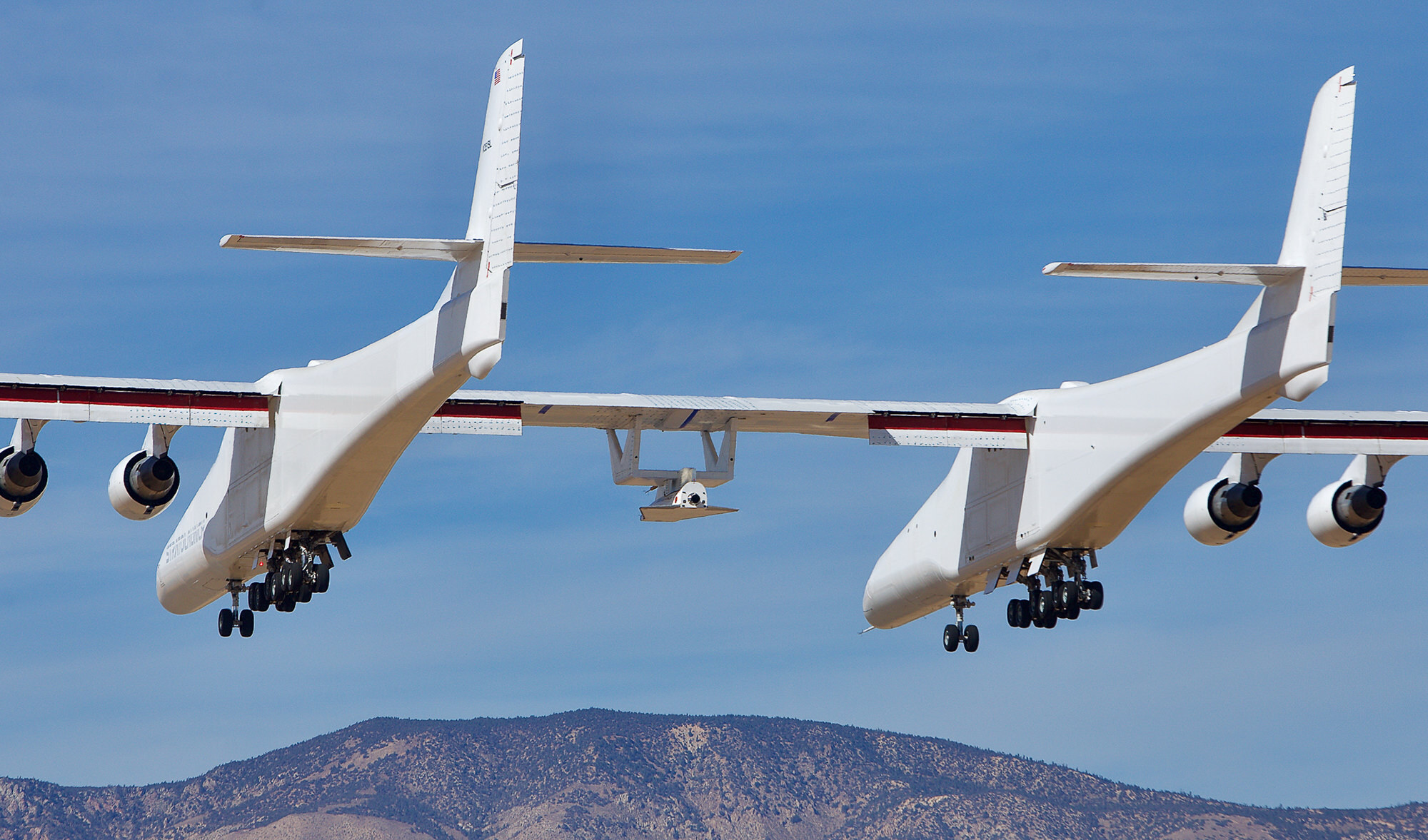
Because of its size, Rainey said that operating the Roc also comes with a pretty significant yaw moment of inertia, which can influence the direction the nose of the aircraft is facing while in flight.
“With low dihedral, there’s lots of adverse yaw,” Rainey said. “So, you put the aileron in and you’re going to get adverse yaw. If you step on the pedal, the opposite is going to be true. There is a great interaction between roll and yaw in this airplane. We have to keep the beta down by controlling that yaw stepping on the pedal, but it’s not what you would think. So, initially, you have to step on the pedal in the direction of the turn, but if you’re not quick to take it out and step the opposite pedal, you’ll get yaw in the other direction.”
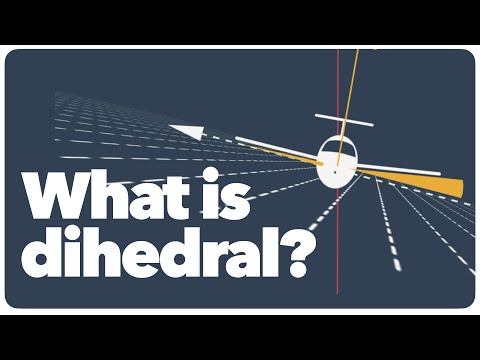
Rainey explains this is the case because the Roc has got a lightly damped dutch roll mode, which is an oscillation that can be described as a combination of sideslip, yawing, and rolling. “[The dutch roll mode] is very controllable. It’s so slow, it’s not that big a deal, but will it affect you on final? Of course, it will, of course,” Rainey said. The Roc can also enter into ‘spiral mode,’ which Rainey explained is when the Roc goes “into a bank, and despite the fact that you’re trying to roll out or keep that bank, it wants to continue to increase bank. So, that is evident at about 15 degrees of bank and becomes pretty nasty at 30 degrees of bank, so our knock-it-off limit is at 35. And we do all of our envelope expansion turns at 30 degrees.”
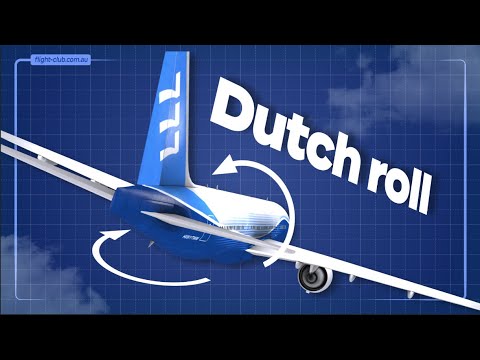
Because of the skills Rainey and his team bring to the Roc’s ongoing flight testing, Stratolaunch is learning in real-time the ins and outs of flying and landing an aircraft of this size and configuration. While that alone is impressive, the Roc’s future in hypersonic testing is hoped to come with it its own trailblazing discoveries.
Even though its mission has evolved since the death of its primary financial backer and visionary, Microsoft cofounder Paul Allen, Stratolaunch has since made it clear that providing a flexible and efficient way to evaluate hypersonic capabilities is its main goal. As mentioned earlier, Stratolaunch plans to do this by using Roc as a launch platform for hypersonic surrogate test vehicles, like its Talon-A.
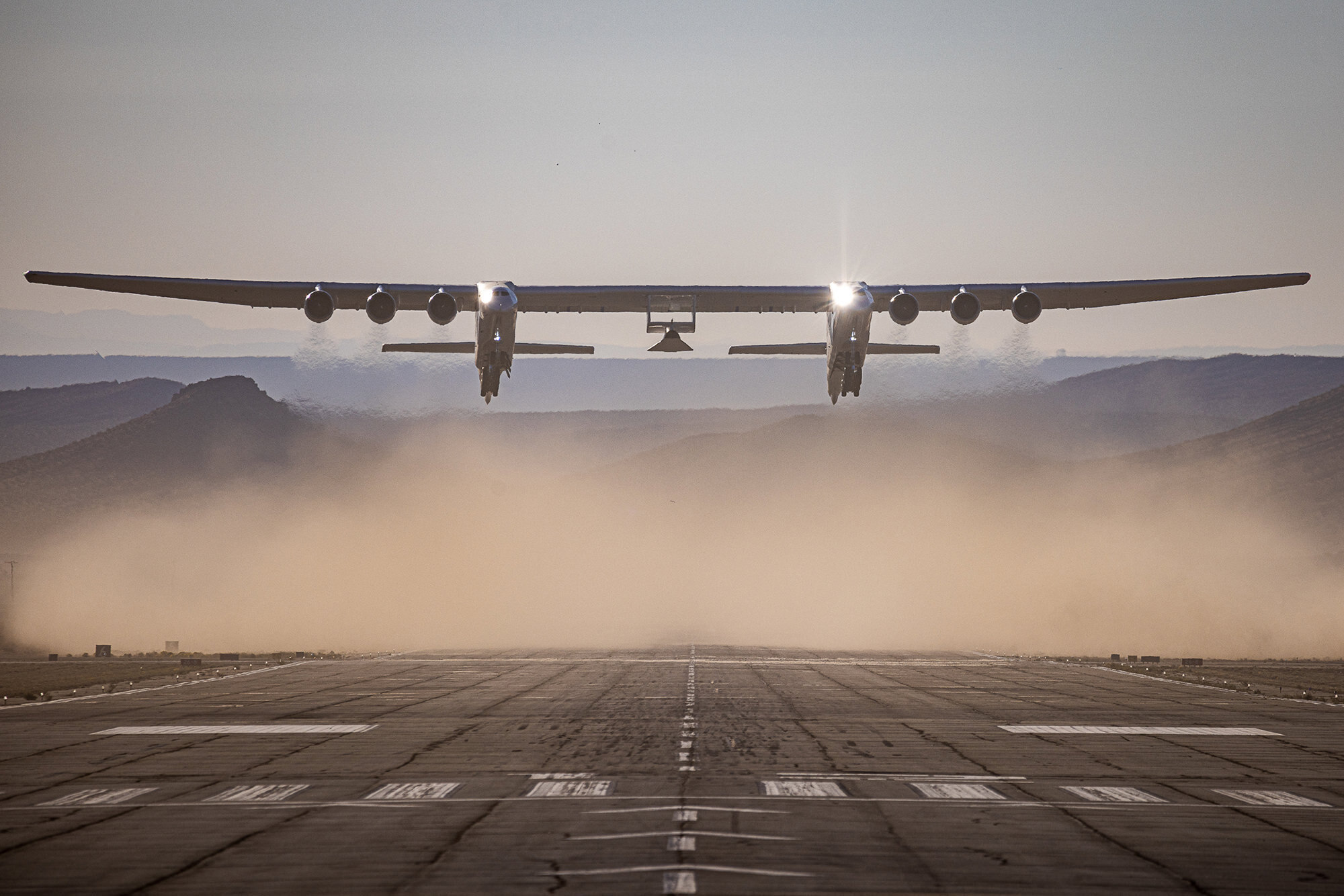
“What we are going to provide is a vehicle that’s big enough for you to put all types of equipment in to be tested at hypersonic speeds, fly at sustained hypersonic speeds for longer durations, and then recover, and land the airplane at Vandenberg Air Force Base,” said Rainey. “So, not only do you get your telemetry data, you’ll have onboard data, which is generally higher quality and higher data rate, and guess what, you get your parts and pieces back to check them out.” One can imagine this as being especially useful for material sciences and integrated sensors and other payloads onto hypersonic vehicles, as well as the aerodynamic side of development.
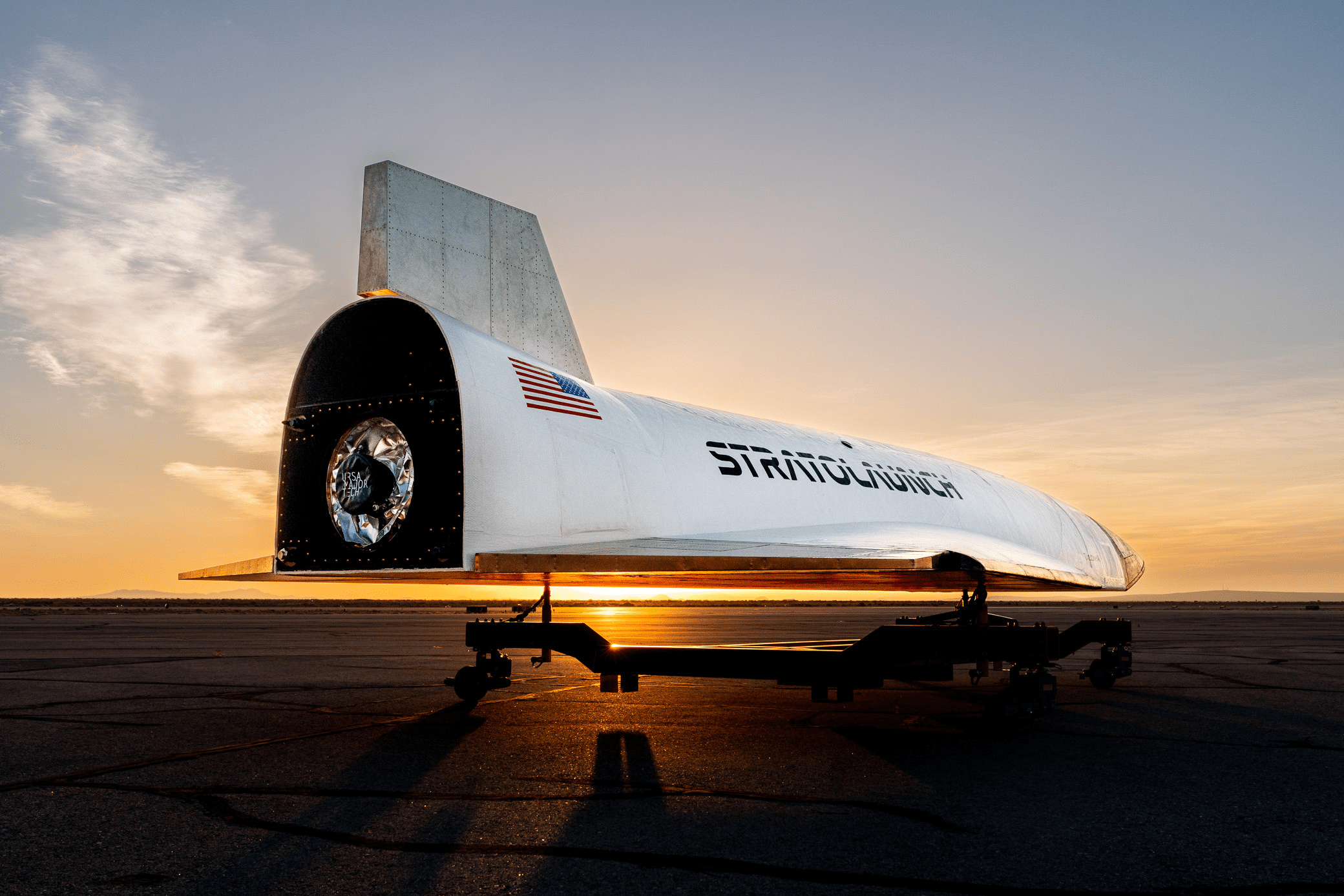
Roc will lift Talon-A and other vehicles, including potentially much larger ones, up to the optimal altitude before releasing them on their test mission. The fact that it acts as a mothership makes it flexible in terms of where it can launch test vehicles and when. But, of course, the first step in achieving these ambitions will be continuing Roc’s own flight testing so it can be certified to carry Talon-A on an operational mission and any potential future hypersonic testbed vehicles.
So there you have it, a fascinating inside look at what it is like flying the world’s largest plane from the guy that is tasked with doing it. Be sure to give Rainey’s whole lecture at the Western Museum of Flight, including the section on testing the F-22, a full watch in the video below:
It’s definitely worth it.

Contact the author: Emma@thewarzone.com