Bell has been quietly flight testing a modified Model 429 helicopter with a new all-electric tail rotor configuration in Canada for months. This Electrically Distributed Anti-Torque system, or EDAT, offers improved efficiency and reliability, as well as a reduced acoustic signature and lower maintenance costs compared to traditional tail rotors.
The Fort Worth, Texas-headquartered helicopter maker brought its EDAT work to the public’s attention when it posted a video montage of the experimental Model 429 on its social media channels on Feb. 20, 2020. However, the video’s caption says that this particular helicopter made its first flight on May 23, 2019. The flight testing has been taking place at Bell’s facility in Mirabel, Quebec.
“In a nutshell, we removed all of the conventional mechanical anti-torque components – which is gearboxes, driveshafts, and tail rotor hub and blades – and replaced it with four electric motors and fans,” Eric Sinusas, Bell’s Light Aircraft Program director, said in an interview with Vertical magazine. “This is the first time anyone in the world ever done this, so the first step was just to make sure that it actually works – and yes it does work.”

A standard Bell Model 429 has an exposed four-bladed tail rotor. All helicopters with a single main rotor require some sort of tail rotor or some other anti-torque system to counteract the force from the large main rotor on top spinning in just one direction.
The EDAT-equipped helicopter replaces the Model 429’s standard tail rotor with four individual four-bladed electrically-powered fans. Each one has its own separate electric motor, provided by French company Safran. They are all built into the tail assembly, similar to helicopters with Fenestron tail rotors. In this configuration, they function as ducted fans.
This modified helicopter’s two Pratt & Whitney Canada PW207 turboshaft engines are linked to generators to provide the requisite power for the EDAT system. In a regular Model 429, the engines are linked mechanically, via driveshaft in the tail boom, to the tail rotor.
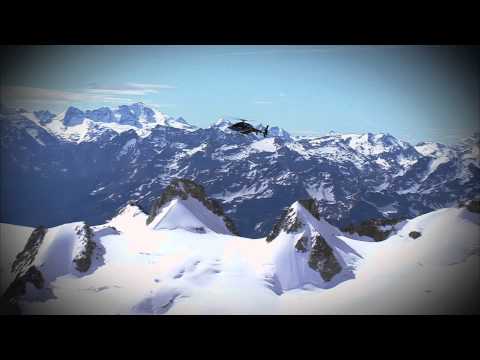
Without that mechanical drive, EDAT relies entirely on a computerized fly-by-wire system to connect the controls in the cockpit to the tail rotors. What this means is that the helicopter can be more efficient than others with traditional tail rotors.
Traditional tail rotors use variable pitch blades to alternate the amount of force they put out and in what direction it is flowing. EDAT’s four rotors have fixed-pitch blades that can spin either forward or backward. Bell says that this means its electrically-powered and controlled system can more precisely and dynamically change how much anti-torque force it’s putting out.
“They are fixed-pitch blades and they’re changing rpm [rotations per minute] constantly,” Bell’s Sinusas told Vertical. “A single large fan or two medium fans are going to experience rotational inertia, so it is going to be less responsive,” he explained to Aviation Week.
Having four fans instead of one single rotor also offers valuable redundancy, which in turn makes the helicopter safer to fly. Bell says that the EDAT system can provide sufficient anti-torque force even if three of the four electric fans fail.
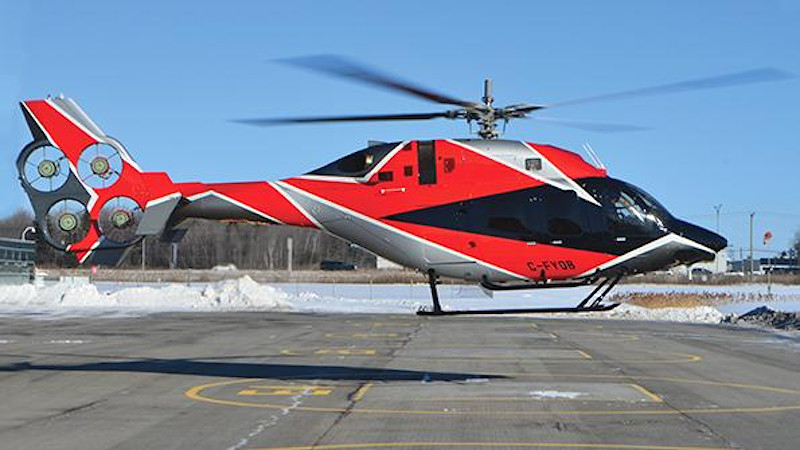
Bell says that the variable speed of the fans and their ability to operate at low RPMs whenever possible also reduces the helicopter’s acoustic signature, though they haven’t yet given specific figures. The information the company has collected so far “shows that it is significantly quieter than a conventional 429,” Sinusas said to Aviation Week.
Lastly, eliminating the conventional mechanically-powered tail rotor would also help lower maintenance costs, by getting rid of the associated potential points of failure in the drivetrain and the tail rotor gearbox. This means maintenance crews wouldn’t have to perform regular inspections of those components or spend time replacing them. Operators wouldn’t have to keep those spare parts on hand anymore, either.
Helicopter companies around the world have been working on electric tail rotors and other anti-torque systems for some time now, but Bell’s is the first to achieve flight, according to Aviation Week. It’s not clear how long the company has been working on this particular project, but it submitted at least one patent application regarding relevant technologies in 2017, approval of which is still pending. The accompanying documents include line drawings that show a variety of notional multi-motor configurations, including variations with ducted fans, as well as exposed rotors. A modified Bell Model 407, rather than a 429, is depicted as the representative helicopter.

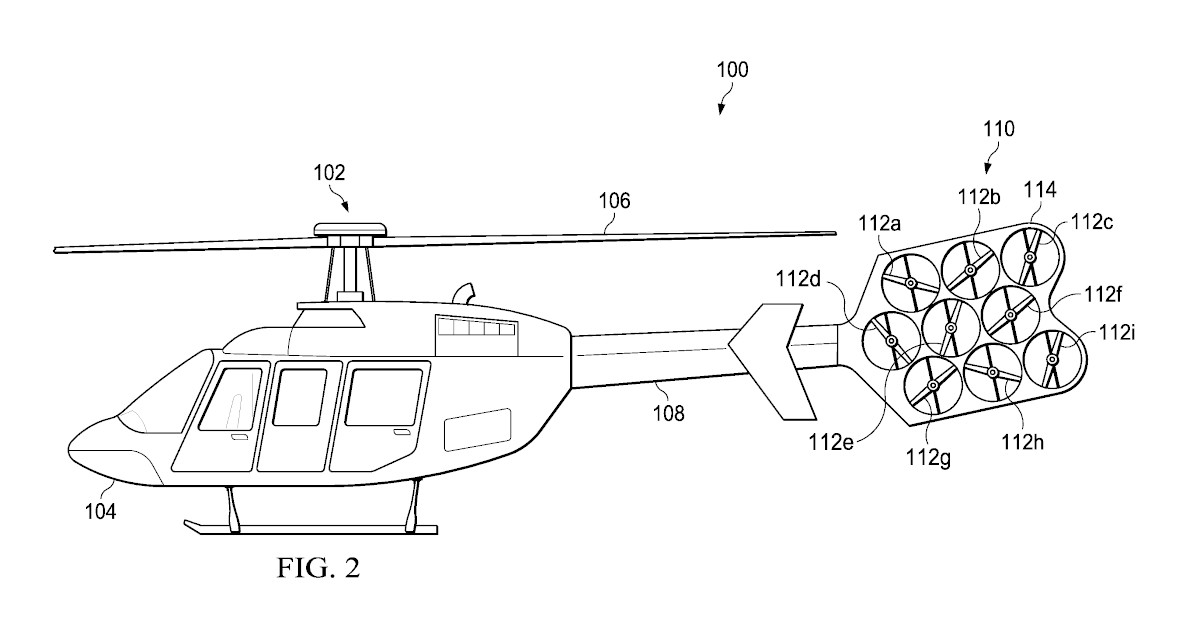
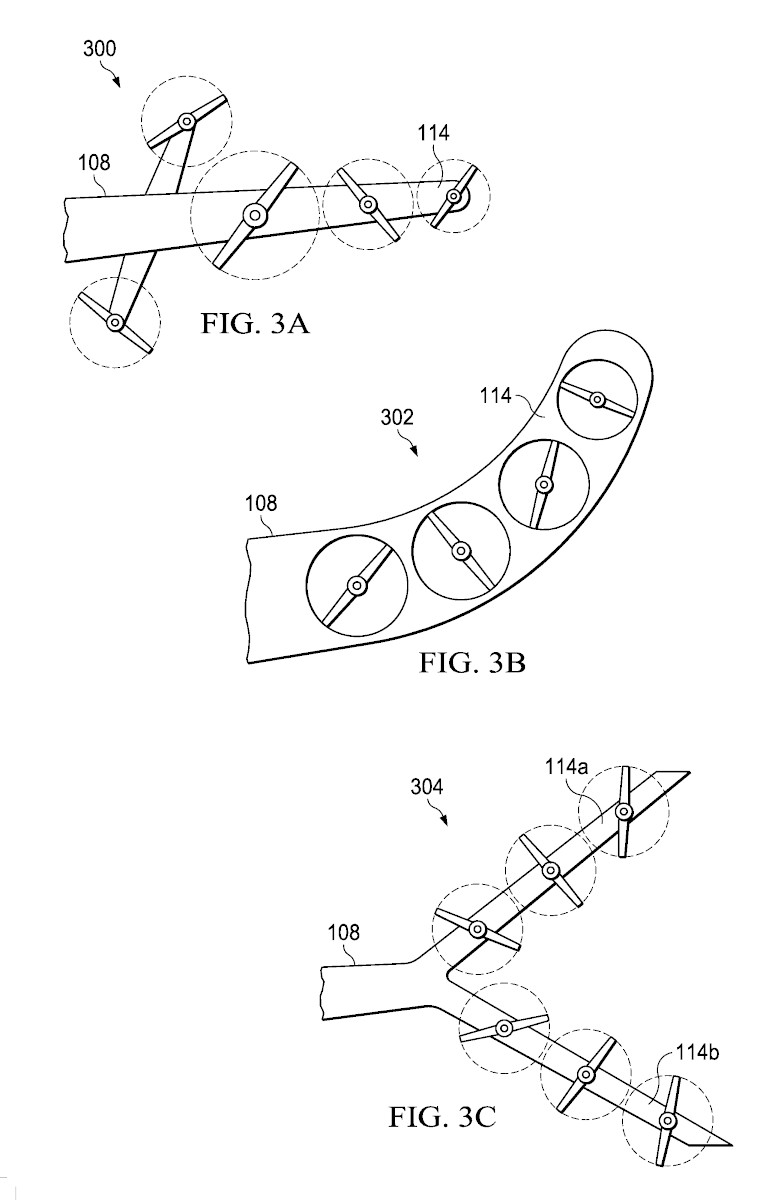
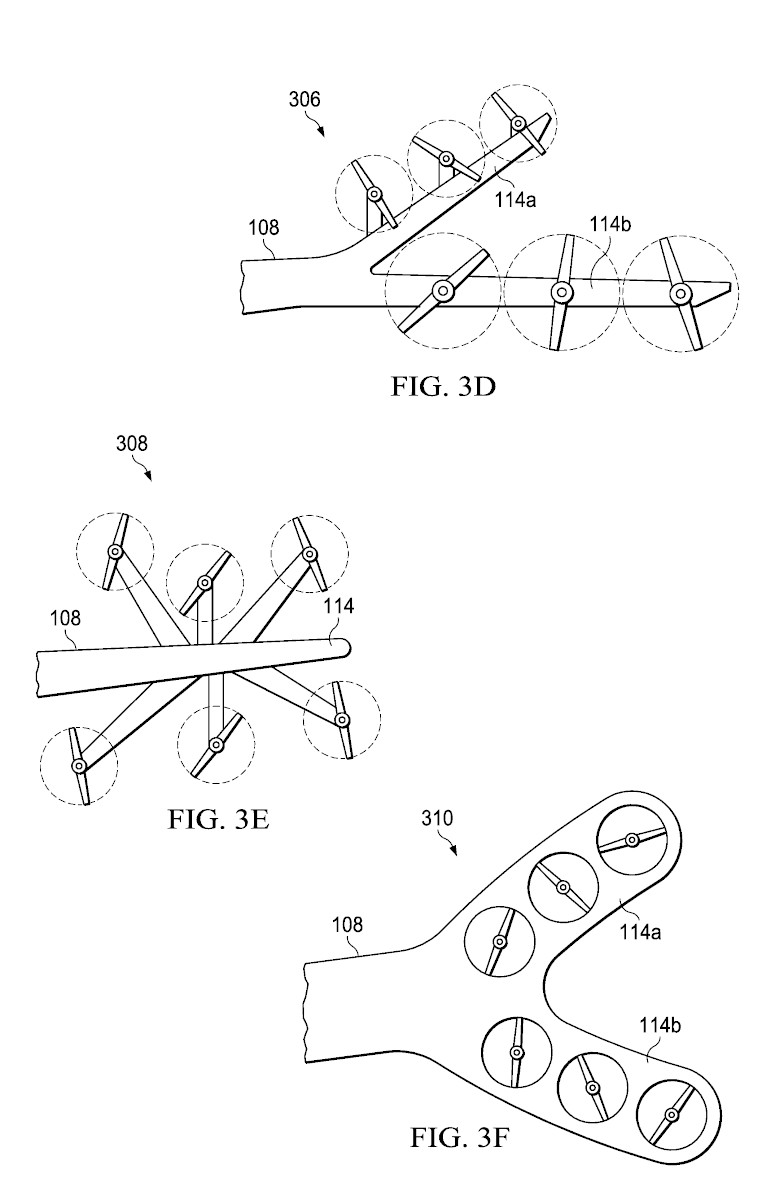
The effort is primarily self-funded. However, Bell did receive grants from authorities in Ottawa in 2018, according to Aviation Week.
The advantages the EDAT system offers could be valuable for civilian, commercial, and military helicopter operators alike. Everyone likes greater efficiency, added safety, and lower operating costs.
The noise helicopters produce often provokes complaints from people living below high traffic routes and means that individuals can hear them coming from relatively far away. A reduced acoustic signature could mean fewer noise complaints for commercial and military operators, as well as help military helicopters better avoid detection during combat operations. Finding ways to reduce tail and main rotor noise has been a major issue in the development of stealthy helicopters. Bell says that customers’ requests for ways to reduce noise, in general, including for occupants, was a major driver in developing EDAT.
The storied helicopter manufacturer states that the EDAT system, as it stands now, is still very much experimental and that it is already working to improve it. The company also views it as a pathway toward future helicopters and other rotorcraft with hybrid or all-electric propulsion. For example, it could help inform work on the Bell FCX-001 experimental helicopter concept, which the company first unveiled in 2017, also includes “electric distribution and motors to drive the anti-torque system.” However, the FCX-001 has a very different configuration for the EDAT-equipped Model 429, with the thrust-vectoring anti-torque system contained entirely within the tail boom that similar, broadly, to Huges Helicopters’ No Tail Rotor (NOTAR) configuration.
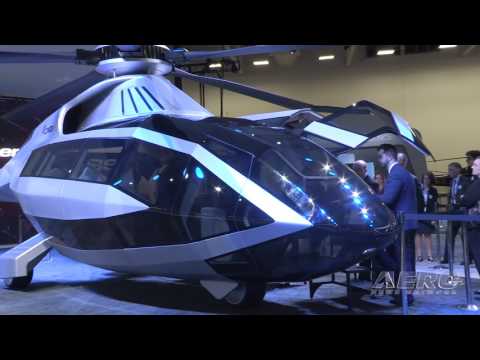
“We have already had several optimizations and changes, just based on feedback from pilots, and it is much quicker to do than with a mechanical system,” Sinusas told Aviation Week. “We do see it as a stepping stone to the fully electric aircraft… We feel like it should make the certification paths for these technologies easier.”
Whether EDAT actually sees widespread use or if it serves simply as a developmental milestone, it is hard to imagine how this concept doesn’t have the potential to change rotary-wing aviation as we know it.
Contact the author: joe@thedrive.com